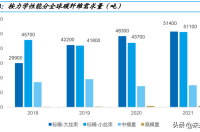
(报告出品方/作者:国金证券,陈屹、王明辉、杨翼荥)
一、碳纤维的性能优异,下游应用广泛
1.1 碳纤维是一种性能优异的材料
碳纤维是由聚丙烯腈、黏胶纤维、沥青纤维等有机纤维在 1000℃以上裂解 碳化形成的含碳量高于 90%的无机纤维,碳纤维呈黑色,其质轻、强度高, 密度仅是钢的四分之一,而强度却是钢的十倍,同时具有易于成型、耐腐 蚀、耐高温等多种优良性质,广泛用于航空航天、风电叶片、汽车工业、 体育休闲等领域。
碳纤维在力学性能方面,兼有碳材料的强抗拉力和纤维的柔软可加工性, 高强度、高模量;在物理性能方面,具有耐高低温、导热、导电、摩擦系 数小和各向异性;在化学性能方面,具有耐腐蚀性。
碳纤维的应用通常呈现为碳纤维复合材料。碳纤维复合材料由基体材料和 增强纤维材料组成,在性能上互相弥补,根据不同的基体材料可分为树脂 基复合材料(CFRP)、碳/碳复合材料(C/C)、金属基复合材料(CFRM)、 陶瓷基复合材料(CFRC)和橡胶基复合材料(CFRR),目前主要以树脂 基复合材料为主,约占全部碳纤维复合材料的 90%以上。
1.2 碳纤维主要以聚丙烯腈基为主
碳纤维按原丝类型可分为粘胶基、沥青基和聚丙烯腈(PAN)基。其中聚 丙烯腈(PAN)基由于其工艺相对简单,性能优良,是目前主流产品,产 量约占全球碳纤维总量的 90%以上,而粘胶基和沥青基碳纤维仍然处于开 发阶段,只有小规模的生产。
碳纤维按照力学性能可分位高强型、高强中模型、高模型和高强高模型, 划分的维度为碳纤维的拉伸强度和拉伸模量。上述标准是我国 2020 年发 布的 GB/T 26752-2020 所规定的聚丙烯腈基碳纤维国家标准,由于日本东 丽在全球碳纤维行业中具有领先优势,业内一般以日本东丽的产品牌号为 基础,将碳纤维产品划定为 T300、T700、T800 等不同级别,国内大部分碳纤维厂商在此基础上确定自身的产品牌号,根据吉林碳谷的年报,随着 我国碳纤维技术的发展,行业整体达到了 T400 的技术能力,部分企业实 现了 T700 碳纤维规模化生产,T800 及以上已经进入了小批量试验生产。 例如中复神鹰相继开发出 T700、T800、T1000、M30、M35、M40 等级 别的碳纤维,光威复材的产品涵盖 T300、T700、T1000、M40J、M55J 等。
碳纤维按丝束大小可分为大丝束和小丝束。目前普遍把每条丝束含有 48000 根以上单丝的碳纤维划分为大丝束,反之为小丝束。小丝束产量低、 成本高,常用于国防军工、航空航天、体育休闲等领域,被称为“宇航级 材料”;大丝束成本低,但生产控制难度大,可广泛用于工业与民用领域, 如风电叶片、压力容器、汽车、轨道交通、建筑补强、海洋工程等,被称 为“工业级材料”。根据赛奥碳纤维的统计,2021 年全球大丝束需求量为 5.14 万吨,小丝束为 5.11 万吨。
1.3 碳纤维应用领域不断拓展
1959 年是碳纤维的元年,UCC 公司生产低模量粘胶基碳纤维,进腾昭男 发明 PAN 基碳纤维,1965 年太谷杉郎发明沥青基碳纤维,日本牢牢抓住 了技术领先的地位;1972 年,碳纤维开始应用于体育领域,鱼竿、高尔夫 相继使用碳纤维;1982 年,随着石油危机引起的航空业降低油耗、追求结 构轻量化需求,碳纤维材料进入到航空航天领域,波音 757、767 以及空 客 A310 相继采用;20 世纪 90 年代以后,随着技术革新,成本的下降, 碳纤维开始应用于船艇、建筑、风电叶片、新能源汽车等领域,进入到了 全面扩张阶段。
2008-2021 年,全球碳纤维需求量逐年增长,2021 年达到 11.8 万吨,年 复合增长率为 9.5%。而在供给端,由于中国产能在近两年大幅扩张,全球 碳纤维产能也水涨船高,2021 年全球运行产能 20.76 万吨,同比增长 20.9%,其中中国产能 6.28 万吨,同比增长 74%。
全球风电叶片对碳纤维需求量最大,航空航天用碳纤维市场规模第一。碳 纤维下游应用领域广阔,主要有风电叶片、航天航空、体育休闲、碳碳复 材和压力容器等领域。从需求量角度看,风电叶片的碳纤维需求最大, 2021 年全球风电叶片用碳纤维需求量为 3.3 万吨,占比 28%,其次为体育 休闲和航空航天,占比分别为 16%、14%。从市场规模来看,航天航空领 域的市场规模最大,2021 年航空航天领域碳纤维市场规模达 11.88 亿美元, 占比 35%,其次为风电叶片和体育休闲,占比分别为 16%、15%。从单价 角度看,风电叶片用碳纤维价格最低,2021 年约为 16.8 美元/公斤,航空 航天用碳纤维价格最高,2021 年约为 72 美元/公斤。
我国碳纤维需求结构中新能源占比高,航空航天与海外差距较大。2021 年 我国碳纤维需求量达到 6.24 万吨,同比增长 27.7%,需求结构中,排名前 四的行业分别是风电叶片、体育休闲、碳碳复材和压力容器,需求量分别 为 2.25 万吨、1.75 万吨、0.7 万吨和 0.3 万吨。近年来,受新能源行业的 拉动,碳纤维在风电、碳碳复材和压力容器领域的需求高速增长,三个行 业需求量的三年 CAGR 分别为 48%、85%、36%,远超其他行业。而在全 球市场规模最大的航天航空领域,我国目前需求量仅 2000 吨,在全球 1.65 万吨的需求体量中占比很小,未来有很大的提升空间。
二、新能源推动碳纤维需求高速增长,航空航天等领域空间广阔
碳纤维因其优异的性能在许多行业皆有渗透,近几年来以风电、光伏和氢 燃料电池汽车为代表的新能源行业正在经历或具备爆发式增长的前景,受 益于风电叶片大型化、光伏硅片大尺寸和氢燃料电池车的大规模量产,碳 纤维在新能源领域的渗透率有望提升,需求将迎来高速增长。在航空航天 领域碳纤维也将受益于商用飞机的复苏、无人机的高增长以及军机换代带 来的需求增长。在交通领域,碳纤维在汽车和轨道交通中的渗透率还有很 大提升空间,尤其是轨道交通有望成为碳纤维未来新的增长点。
2.1 风电叶片:受益于叶片轻量化与海风发展,碳纤维需求有望高速增长
清洁能源政策推动,风电未来发展空间巨大。全球多个国家和地区鼓励发 展风电产业,根据全球风能理事会(GWEC)统计数据,全球风电累计装 机容量从 2012 年的 283.2GW 增至截至 2021 年的 837.5GW,年复合增长率为 12.8%。我国风电累计装机容量从 2012 年的 60.6GW 增至 2021 年 的 328.5GW,年复合增长率为 20.7%,增长率位居全球第一。GWEC 预 计,到 2026 年,全球和我国风电累计装机量将分别达到 1394GW 和 617GW,近五年 CAGR 分别为 10.7%和 13.4%。尽管全球风电装机量快 速上升,但 GWEC 预计,按当前的发展速度,到 2030 年,全球风电装机 容量将不足《巴黎协定》设定的在本世纪将升温幅度限制在 1.5℃以内目标 及净零排放路径所需容量的 2/3,无法实现气候目标。在全球环保政策推动 下,风电未来发展空间巨大。
风机降本需求推动叶片大型化,从而带动碳纤维需求增加。降低风机成本 是使风力发电成为有竞争力发电选择的必由之路,根据理论发电量的计算 公式,风电机组产生的电能与叶片长度的平方成正比,增加叶片长度可以 带来较为可观的发电量提升,而大容量机组搭配长叶片,能够减少同等装 机规模项目所用的机组数量,相应降低机组及其施工安装等方面的投入。 因此,风机叶片的大型化被视为增强风电机组捕风能力以及降低风电项目 成本的主要途径之一。随着叶片长度的增加,对于材料强度及刚度性能要 求具有更高的标准,研究表明,碳纤维的密度比玻璃纤维低 30%-35%,应 用碳纤维可使叶片减重 20%以上,碳纤维的拉伸模量比玻璃纤维高 3-8 倍, 因此未来大型叶片的碳纤维用量将进一步增长。根据赛奥碳纤维的统计, 2021 年全球风电市场碳纤维用量在 3.3 万吨,预计到 2025 年将增长到 8.1 万吨,四年 GAGR 达 25%。
风电由内陆向海上转移,碳纤维渗透率有望进一步提升。海风相较于陆风, 具有发电量高、靠近负荷中心便于消纳、不占用土地等优势,随着海风成 本的快速下降,未来海风在风力发电中的地位有望快速提升,GWEC 预计, 2026 年全球的海风累计装机量将达到 147.8GW,五年 GAGR 达 20.9%, 海风在风电中的占比将由 2021 年的 6.8%提升至 2026 年的 10.6%。在国 内,由于 2022 年起海风的国家补贴政策正式退出,2021 年我国海风新增 装机容量达到了创纪录的 16.9GW,2022 年后预计每年的海风装机会有下 滑,但根据地方多个省份提出的“十四五”的海风装机规划以及部分省份 的海风补贴计划,预计 2022-2025 年我国海风装机仍会有较大增长,根据 GWEC 预测,到 2026 年我国海风装机量将达到 66.7GW,五年 GAGR 达 19.2%。相对于陆风机组,海风机组大型化的降本作用更加明显,根据 Rystad Energy 的研究项目推算,对于 1GW 的海上风电项目,采用 14MW 的风电机组将比采用 10MW 风电机组节省 1 亿美元的投资。因此海 风机组将更有动力使用大叶片,从而进一步提升碳纤维的渗透率。
VESTAS 拉挤梁工艺使得大丝束碳纤维广泛应用于风电叶片,专利到期利 好国内拉挤碳梁发展。从经济的角度考虑,VESTAS 的拉挤碳梁工艺是碳 纤维得以在风电叶片中大幅推广的重要工艺。2015 年以前,碳纤维应用在 风电叶片的工艺主要采用预浸料或织物的真空导入,部分采用小丝束碳纤 维,导致成型叶片价格偏高,2015 年以后由 VESTAS 发明的叶片拉挤梁 工艺也使得成本更低的大丝束碳纤维广泛应用于风电叶片,目前维斯塔斯 兆瓦级以上风机叶片都使用碳纤维复合材料,极大的推动了碳纤维在风电 领域的应用。根据赛奥碳纤维的数据,2022 年在风电领域,VESTAS 和 GE 的碳纤维板材用量预计维持在 3 万吨,其他企业如 GAMESA、NorDex, 明阳、三一、上海电气等的用量预计为 3500-4500 吨。在价格方面,2015年风电用碳纤维价格为 23 美元/公斤,到了 2016 年以后,价格就稳定在 14 美元/公斤左右。近两年中材科技、时代新材、中复连众、艾朗等叶片厂 家以及主机厂三一重工、明阳电气、上海电气等都陆续发布了使用碳纤维 或碳玻混合拉挤大梁叶片,2022 年 7 月 19 日,随着 VESTAS 拉挤梁专利 保护到期,国内拉挤碳梁需求有望快速上升。
叶片大型化与海风的发展推动国内碳纤维需求增长,预计 2026 年国内风 电叶片用碳纤维需求量达 5.7 万吨。根据赛奥碳纤维的统计,2021 年我国 风电叶片碳纤维需求量为 2.25 万吨,同比增长 12.5%,占全球风电叶片用 碳纤维需求的 68.2%。随着 2022 年以后我国风电上网全面取消中央补贴, 风电产业将逐步步入平价上网时代,为了降低度电成本,我国风电机组将 继续向大型化方向发展,同时各省对海风的补贴也在陆续跟进以实现海风 平价上网的平稳过渡。根据 GWEC 的预测,到 2026 年我国陆风累计装机 量将达到 550GW,海风累计装机量将达到 67GW,根据我们的测算,届 时国内风电叶片用碳纤维需求量将从 2021 年的 2.25 万吨增至 2026 年的 5.69 万吨,五年 CAGR 达 20.4%。
2.2 碳碳复材:光伏装机增长与单晶炉扩容助力碳纤维需求高速增长
光伏行业大规模步入平价上网时代,未来装机量将保持高速增长。近年来 光伏行业技术不断提升,转换效率不断提高,光伏发电成本快速下降, 2020 年以来,光伏行业进入快速发展的平价上网新时期。未来,在光伏发 电成本持续下降和全球绿色复苏等有利因素的推动下,全球光伏新增装机 仍将快速增长。CPIA 预计,“十四五”期间,全球光伏年均新增装机将超 过 240GW,中国光伏年均新增装机将超过 70GW,我国发改委的《“十四 五”可再生能源发展规划》也计划在“十四五”期间,实现风电、光伏发 电量翻番,CPIA 预计,到 2025 年,在乐观和保守假设下,我国光伏累计 装机量将分别达到 682GW 和 607GW,四年 CAGR 达 22.1%和 18.6%。
单晶炉扩容助碳碳复材渗透率提升,碳纤维需求有望迎来高增长。碳碳复 材是由碳纤维及其织物增强碳基体所形成的高性能复合材料。该材料具有 比重轻、热膨胀系数低、耐高温、耐腐蚀、摩擦系数稳定、导热导电性能 好等优良性能,是制造高温热场部件和摩擦部件的最佳候选材料。在光伏 领域,碳碳复材主要应用于光伏用单晶硅拉制炉热场系统,主要产品包括 坩埚、导流筒、保温筒、加热器等。随着光伏行业发展,单晶硅拉制炉容 量快速扩张,已从 2011 年左右的 16 英寸-20 英寸热场快速发展到现在的 32 英寸和 36 英寸,而传统的等静压石墨作为由石墨颗粒压制成型的脆性 材料,已经在安全性方面不能适应大热场的使用要求,在经济性方面也已 经落后于碳基复合材料,因此碳碳复材在单晶炉中的渗透率有望进一步提 升。根据金博股份招股书,到 2020 年,碳基复材制成的坩埚、导流筒、 保温筒、加热器的渗透率已分别处于 95%、60%、55%、5%的水平。
光伏装机增长与单晶炉扩容助力碳纤维需求高速增长,预计 2025 年我国 碳碳复材市场碳纤维需求量达 13700 吨。未来光伏硅片行业将迎来装机高 增长与硅片大尺寸的双重趋势,大直径单晶硅棒的拉制需要具备更大尺寸 的热场以及更大规格的装料系统,单晶炉热场部件的直径在未来将进一步 增大,伴随碳碳复材在热场部件中的渗透率提升,碳纤维用量将高速增长。 碳碳复材市场按照下游需求可分为刹车盘市场、航天部件市场和热场部件 市场,赛奥碳纤维估计 2021 年我国碳碳复材市场对碳纤维的总需求为 7000 吨,根据本文测算,2021 年-2025 年,我国热场部件用碳纤维需求 量有望从 3400 吨增长至 8400 吨,若假设期间刹车盘市场和航天部件市场 的碳纤维需求以每年 10%的增速稳步增长,则到 2025 年,我国碳碳复材 用碳纤维需求有望达到 13700 吨,四年 CAGR 达 18%。
2.3 压力容器:氢燃料电池车推广加快,储氢瓶用碳纤维需求高速增长
政策推动下氢燃料电池车行业步入快车道,2022 年将是氢能及燃料电池行 业的爆发元年。氢燃料电池车具有零排放、销量高、运行平稳、耐低温、 续航稳定等诸多优点,是对电动汽车很好的补充,并可有效促进我国电力 行业清洁化转型,更大程度助力碳中和目标。2021 年底,随着河南、河北 两大燃料电池汽车示范城市群的启动,全球“3+2”燃料电池汽车示范格 局形成,按照规划,在 4 年示范期内,5 大示范区预计推广各类氢燃料电 池汽车 3.3 万辆。今年三月,发改委发布了《氢能产业发展中长期规划 (2021-2035 年)》,规划到 2025 年,燃料电池车辆保有量约 5 万辆。根 据中汽数据统计,2021 年,我国氢燃料电池车销量达到 1881 辆,2022 年 1-6 月,我国燃料电池车销量已超过 1400 辆,根据国金证券新能源与汽车 研究中心的预计,下半年燃料电池单月装车量有望超千辆,氢燃料汽车开 始步入大规模量产时期。
重卡是氢燃料电池推广的重要场景,销量有望大幅增长。在重卡领域,氢 燃料电池具有长续航、低排放的优势,长期而言相较锂电池和柴油机具有 明显优势,被认为是最适合氢燃料电池车优势的应用场景。根据中汽数据 和高工锂电的数据,2021 年我国氢燃料电池重卡销量达到 779 辆,在专用 车中占比高达 94%,较 2020 年的 20 辆有质的增长,赛奥碳纤维预计 2022 年我国氢燃料电池重卡销量有望达到 6000 辆,在未来会成为氢燃料 汽车增长的重要动能。
氢燃料电池汽车高速增长推动车载储氢瓶用碳纤维需求提升,预计 2025 年我国压力容器用碳纤维需求量约 6600 吨。压力容器用碳纤维主要应用 于呼吸气瓶、CNG 气瓶和储氢气瓶中。在储氢领域,氢燃料电池汽车主要 使用金属内胆碳纤维全缠绕气瓶(III 型)和塑料内胆碳纤维全缠绕气瓶 (IV 型)作为车载储氢瓶,碳纤维缠绕在气瓶的内胆外围,以增加内胆的 结构强度。根据高工锂电的统计,目前客车常配置单套 6-8 瓶组,单瓶 140L 或 165L 的储氢系统;轻、中卡多配置单套 2-4 瓶组,单瓶 140L、 165L 或 260L 的储氢系统;12 吨-18 吨中、重卡多配置 6-8 支 165L/210L 储氢系统;31 吨-49 吨重卡多配置 6-8 支 210L 车载储氢系统;乘用车多配 置 2-4 瓶组,单瓶 65L 储氢系统。根据奥赛碳纤维的估算,一辆重卡的碳 纤维用量在 240-360 公斤,其他类型商用车碳纤维单车用量在 150 公斤左 右,而根据乘用车用的气瓶体积,我们估计乘用车的碳纤维单车用量约在 50 公斤左右。未来随着氢燃料电池汽车尤其是重卡的快速增长,我们预计 到 2025 年,我国储氢气瓶用碳纤维需求量约为 4250 吨,呼吸气瓶和 CNG 气瓶假设需求假设每年以 10%的速度增长,则到 2025 年,我国压力 容器用碳纤维需求量将达到 6590 吨,四年 CAGR 达 21.7%。
2.4 航空航天:碳纤维应用广泛,需求空间巨大
碳纤维由于具有质轻、高强度、耐热耐疲劳的属性,在航空航天领域有广 泛应用。在航空领域,碳纤维相对于钢或铝,减重效果可以达到 20%至 40%,主要应用于飞机的结构材料(占飞机重量的 30%左右),能使飞机 重量减轻 6%至 12%,从而显著地降低飞机的燃油成本,所以碳纤维在航 空航天领域中,商用飞机占比近 35%。此外,随着无人机数量的快速增长, 碳纤维在无人机领域的需求占比也在 2021 年迅速提升至 21%。我国第五 代战机的规划化列装也加速了国产碳纤维在军工飞机中的应用。在航天领 域,由于其耐热耐疲劳的特性,碳纤维用于人造卫星的天线和卫星支架的 制造,以及固体火箭发动机壳体和喷管。
碳纤维在客机渗透率逐年提高,客机订单疫情后有望逐步恢复。碳纤维是 飞机上最常用的复合材料,20 世纪 80 年代,碳纤维复合材料开始应用于 客机的非承力构件,早期如空客 A310、波音 B757 和波音 B767 的碳纤维 渗透率仅为 5%-6%,随着技术的不断进步,碳纤维复合材料逐渐作为次承 力构件和主承力构件应用在客机上,空客 A380 的碳纤维渗透率达到 23%, 应用于主承力结构部件如主翼、尾翼、机体、中央翼盒、压力隔壁等,次 承力结构部件如辅助翼、方向舵及客机内饰材料等,开创了先进复合材料 在大型客机上大规模应用的先河。而波音 B787 和空客 A350 碳纤维渗透 率达 50%以上,有更多部件使用碳纤维,例如机头、尾翼、机翼蒙皮等, 使用量大大提升。近两年受疫情和 B787 因生产缺陷暂停交付的影响,商 用飞机用碳纤维需求量较以前年度大幅下滑,根据赛奥碳纤维的数据, 2021 年全球商用飞机碳纤维需求量为 5800 吨,同比下滑 33.3%。2022 年以后随着疫情的修复与 B787 的恢复供应,商用飞机市场预计缓慢复苏。
ARJ21、C919、CR929,国产商用飞机碳纤维渗透率逐级提升。我国商 用客机使用碳纤维经历了一个渐进的过程。ARJ21 是我国首款喷气支线客 机,其复合材料用量在 2%左右,主要应用于方向舵和翼梢小翼等部位。 该机型于 2016 年实现商业运行,至今已交付近 70 架。C919 作为我国首 款大飞机,其复合材料用量在 12%左右,应用部位包括了水平尾翼、垂直 尾翼、翼梢小翼、后机身、雷达罩、副翼、扰流板和翼身整流罩等,也是 我国首款使用 T800 高强碳纤维增强复合材料的民用飞机。目前 C919 累计 获得 28 家客户包含确认订单和意向订单在内的 815 架订单,预计 2022 年 进入商业化阶段。CR929 是中国商用飞机计划研制的首款大型远程宽体客 机,预计其复合材料占比将达到 50%以上,与 A350 和 B787 属于同一量 级,应用部位包括机身、机翼和尾翼。该机型预计 2023 年前完成首飞并 在 2025 年前完成试航取证并交给首个用户。对于 C919,我们假设它到 2025 年具备年产 50 架的能力,单机的空机重量约为 42.1 吨,碳纤维复合 材料占比 12%,则对应的碳纤维需求量约为 125-200 吨。根据中复神鹰的 估计,C919 对国产 T800 级碳纤维需求量是 100 吨/年,随着 CR929 的研 发推进,CR929 对国产 T800/T1000 级碳纤维需求量将跨越式增长。
无人机碳纤维使用率高,未来需求高增长。无人机不论在军用领域,还是 空中摄影、气象观察等民用领域,都越来越被广泛使用。根据 Preference Research 统计,2021 全球无人机市场规模在 226.8 亿美元,预计到 2030 年达到 1023.8 亿美元,年复合增长 18.2%。根据观研报告的数据,2021 年中国民用无人机市场规模达 869.12 亿元,同比增长 45.1%,预计到 2024 年我国民用无人机市场规模将达到 2075 亿元,年复合增长 33.7%。 无人机碳纤维使用率高,根据《先进复合材料在无人机上的应用及关键技 术》,碳纤维复合材料在各国无人机的结构质量占比在 60%-80%,使机体 质量减轻 25%以上,美国全球鹰无人侦察机使用复合材料达 65%,X-45C、 X-47B、“神经元”、“雷神”等达为 90%。我国“彩虹 4”无人机使用复合 材料达到 80%。根据赛奥碳纤维的统计,2021 年全球无人机用碳纤维需 求量为 3450 吨,较 2020 年的 750 吨大幅增长,随着无人机的推广使用, 未来碳纤维在该领域的需求有望高增长。
军用飞机高性能要求和高成本接受度,推动碳纤维技术发展。军机上广泛 使用碳纤维复合材料可以减轻重量,从而显著高其作战能力。从 1969 年 起,美国 F14A 战机碳纤维复合材料用量仅为 1%,如今美国 F-22 和 F35 为代表的第四代战斗机上碳纤维复合材料用量达到 24%和 35%, B-2 隐身 战略轰炸机更是超过了 40%。如今,世界各国的军用飞机结构中都采用了 以碳纤维为代表的复合材料,其用量占整个军用飞机质量的 20%~50%。 军用飞机对于飞机性能要求更高,同时可以接受更高的成本和更漫长的研 发制造,在一定程度上,军用飞机对于碳纤维复合材料的应用推动了整个 碳纤维技术的发展,以及在客机方面的使用。
我国军用飞机与美国存在差距,更新换代加大碳纤维使用力度。我军战斗 机以二代和三代机为主,老式战机占比较高,而武装直升机数量 912 架, 仅为占美国武装直升机的 17%(5463 架)。我国三代机碳纤维占比约为 3%,四代战机歼-20 复合材料占比大幅提升至 27%,与美国第四代战机 30%的平均碳纤维用量相接近。根据飞行国际的数据,我国约 60%的军用 飞机面临退役,这将在很大程度上推动军用飞机的需求,将拉动对高端碳 纤维复合材料的需求。
我国航天实力强大,未来发射计划带动碳纤维复合材料运用。航天飞行器 的重量每减少 1 公斤,就可使运载火箭减轻 500 公斤,因此,在航空航天 工业中普遍采用先进的碳纤维复合材料。美国、欧洲的卫星结构质量不到 总重量的 10%。近年来,中国航天发射迈入高密度发射阶段,2021 年我 国共计完成航天发射任务 55 次,据世界首位,2022 年,中国航天计划发 射次数将达 60 次以上,未来航天事业的发展,势必带动碳纤维复合材料的 进一步运用。
2.5 轨道交通:碳纤维推广障碍相对较小,未来潜力较大
高速铁路迅猛发展,贡献数亿市场空间。2021 年底,我国铁路营业里程突 破 15 万公里,其中高铁超过 4 万公里,具有世界上最现代化的铁路网和最 发达的高铁网。国家《“十四五”铁路发展规划》指出:到 2025 年,铁路 网规模达到 16.5 万公里左右,其中高速铁路 5 万公里左右,网络覆盖进一 步扩大,路网结构更加优化。
轨道交通领域碳纤维推广难度较低。轨道交通成本敏感性相对较低,碰撞 可能性低,也不存在维修和保险的问题,而且标准化程度高,对于个性化 设计的要求低于汽车。随着关键技术的提升,轨道交通行业平台化的发展, 碳纤维在轨道交通领域的应用前景广泛。
国内碳纤维复合材料在轨交领域应用起步较晚,但研发进展迅速。当前我 国碳纤维复合材料已完成了次承载件和零部件的研制与应用,诸如高速列 车司机室头罩、裙板、受电弓导流罩、内饰板, 低地板车的侧墙和顶板, 城 轨车辆司机室头罩、司机台, 城际动车组裙板等。我国复兴号已经在车体局 部结构件、车厢侧壁板等部位中使用碳纤维复合材料,假设其单节车厢车 身与饰品所需碳纤维为 2-3 吨,每年新增 100 列、每列 8 节车厢,碳纤维 渗透率 30%计算,则未来每年复兴号所贡献的碳纤维需求量可达 480-720 吨。
城市轨道交的碳纤维应用有望得到加强。碳纤维复合材料能够适应轨道交 通对制造材料隔声、隔热、防火、振动等的要求,日本、德经国已有不少 将碳纤维材料应用于轨道交通车体。截至今年上半年,我国已有累计 51 个 城市投运城际轨道交通线路 9573 公里,未来碳纤维的应用也将得到进一 步加强。2021 年 1 月和 7 月,中国中车研制的时速 200、600 公里的磁悬 浮列车亮相,车型广泛使用了碳纤维材质,预计未来城际轨道领域将带动 碳纤维应用的新爆发点。
2.6 汽车:空间广阔,成本问题制约其推广
汽车用碳纤维需求稳定增长,I3 停产对需求影响较大。碳纤维增强复合材 料可使汽车的总质量比使用钢结构作为主要制造材料减重 50%以上,比铝、 镁合金结构减重 30%以上,有利于提升汽车的节能、加速以及制动等性能,在汽车的车身、刹车片、轮毂、传动轴等部位均有应用。近年来,碳纤维 在汽车中的应用增长较为平稳,2021 年受全球唯一两款大面积采用碳纤维 的宝马 I8 与 I3,分别在 2020 年底与 2021 年中停产的影响,全球汽车用 碳纤维需求量下滑 3000 吨至 9500 吨。
成本问题是制约碳纤维推广的主要因素。汽车是在主体结构采用钢材的基 础上进行轻量化,在碳纤维之外还有铝合金等成本更低的材料可以选择。 据测算,车用碳纤维的减重效果为 50%-70%,铝合金为 30%-60%;车用 碳纤维的密度为 1.5g/cm3,铝合金密度为 2.7g/cm3。因此若分别使用碳纤 维和铝合金材料来达到相似的减重效果,铝合金用料是碳纤维的两倍,而 价格方面,车用碳纤维目前约为 140 元/kg,远高于铝合金的价格。未来随 着技术的不断进步,在碳纤维成本下降至主流车企可接受区间时,碳纤维 可能在汽车领域大规模推广。
三、我国碳纤维产能快速扩张,大丝束成为重要方向
3.1 中国碳纤维产能快速扩张,供需矛盾有望缓解
全球碳纤维产能主要集中在中国、美国和日本,中国产能快速扩张。2021 全球碳纤维产能约 20.76 万吨,其中中国大陆、美国和日本分列前三位, 运行产能分别为 6.34 万吨、4.87 万吨和 2.5 万吨,三家合计占全球产能的 66%。2020-2021 年中国产能快速扩张,两年产能同比增速分别达到 36% 和 74%,我国碳纤维的自给率也从 2015 年的 14%提升至 2021 年的 47%。 国内龙头企业依托成熟的技术以及完备的产业链支持,不断向国际头部企 业看齐。
日本、美国、欧洲碳纤维产业发展较为完善,日本东丽为全球龙头。全球 除中国大陆以外的 PAN 基碳纤维供应商主要有八家,其中日本三家,分别 是东丽、三菱和东邦,美国两家,分为为赫氏和氰特,其他地区三家,分 别为土耳其的阿克萨集团、德国的西格里碳素和中国台湾的台塑。日本碳纤维在技术和产品品质方面居于领导地位,近些年通过超强的技术与融入 全球产业生态的能力,在全球寻求综合优势的区域建厂,使其保持了全球 领导地位;美国的综合投资环境较好,生产要素具有全球优势,产业链生 态完备,航空航天、汽车、风电等方面的应用能力强;欧洲产业链生态完 备,在风电、汽车领域的市场庞大,此外,处于匈牙利及土耳其的碳纤维 企业具备腈纶工业基础,碳纤维产业发展较为完善。日本东丽是全球综合 实力第一的碳纤维企业,早在上世纪 80 年代便有销售 T1000 级的高强碳 纤维,在小丝束领域技术大幅领先,2014 年收购美国卓尔泰克后在大丝束 领域也拥有了成熟产品,2021 年东丽的产能达 5.75 万吨,位居全球第一。
今明两年国内碳纤维进入投产高峰期,供需矛盾有望缓解。2021 年中国大 陆的碳纤维运行产能为 6.34 万吨,占全球的 31%,未来几年,国内仍将 有大规模的扩产计划,其中规模较大的项目例如吉林化纤集团近两年先后 开启的 20 万吨和 40 万吨的碳纤维全产业链项目(其中碳纤维规划分别为 5 万吨和 6 万吨),中复神鹰在西宁建设的 2.4 万吨碳纤维项目,上海石化 1.2 万吨 48K 大丝束碳纤维项目等。赛奥碳纤维估计,未来中国大陆仍将 有 9 万吨的产能增量,届时产能将占全球的 50%以上,根据我们的统计, 2022-2023 年国内待投项目的名义产能分别为 4.28 万吨和 3.55 万吨(不 考虑投产节奏),今明两年即为投产高峰期,产能的大幅投放也将缓解去年 由疫情和进口扰动带来的供需缺口,今年下半年以来,国内碳纤维价格也 出现下滑趋势,预计未来国内供需矛盾将进一步缓解。
3.2 我国大丝束实现技术突破,成为未来重要发展方向
大丝束的制备难度更高,但成本更低,适用于工业民用领域。大丝束和小 丝束碳纤维有不同的工艺难点和优势,小丝束的工艺难点在于它需要更精 准的控制工艺来保证力学指标的稳定,优势在于力学指标更高,可广泛应 用于对于强度要求较高的高端领域,主要应用于军工、航空航天等领域。 大丝束的制备难度整体高于小丝束,在原丝、聚合、预氧化、碳化等多个 系统环节都存在制备难点,但因其生产效率高,生产成本比小丝束低 30% 以上,性能可满足工业民用需求,在风电叶片、压力容器、汽车、轨道交 通等工业领域具备应用前景,并且随着其性价比的进一步提升,未来大丝 束的工业应用方向也有望扩大。
大丝束碳纤维在海外集中度高,近几年国内实现重要技术突破。大丝束碳 纤维主要借鉴民用腈纶原丝技术并优化提升,上世纪 70 年代,英国考陶尔 兹(Courtaulds)公司利用纺织用腈纶生产线研制 48K 以上聚丙烯腈大丝 束原丝取得成功,大丝束碳纤维的技术在欧美得到推广,日本企业则通过 对欧美企业收购的方式掌握了大丝束的技术。目前,海外大丝束碳纤维生 产商主要有卓尔泰克(2014 年被东丽收购)、德国西格里、英国考陶尔兹 等企业,集中度很高。近几年,国内以上海石化和吉林化纤为代表的,具 有腈纶生产经验的企业,逐步突破大丝束的原丝和碳丝的制备技术,2018年 3 月,上海石化成功试制出了国内真正意义上的 48K 大丝束碳纤维,并 于 2021 年 1 月开启“2.4 万吨/年原丝、1.2 万吨/年 48K 大丝束碳纤维” 项目;吉林碳谷与 2018 年实现了 24K、25K 碳纤维原丝的规模化生产, 于 2019 年实现了 48K 原丝的规模化生产,当前已投产万吨级 50K 的原丝 产线;吉林宝旌于 2016 年开启“8000 吨大丝束碳纤维项目”,2018 年采 用吉林碳谷 48K 的原丝成功实现 2000 吨产线的投产。
大丝束成为我国未来碳纤维扩产的重要方向,风电等领域有望迎来国产替 代。2021 年以来,国内以大丝束为方向的产能规划进入了规模化释放阶段, 根据我们对近几年已投、待投碳纤维项目的统计,2021 年-2023 年间,大 丝束的新增名义产能分别占国内当前新增名义产能的 58%、93%、61%, 大丝束已成为我国碳纤维发展的重要方向,从而在与大丝束相关的风电叶 片、压力容器、轨道交通、汽车轻量化等领域有望实现国产替代,例如吉 林宝旌的 8000 吨大丝束项目便与 Vestas 签订了长期供货协议。
3.3 我国高性能碳纤维持续突破,政策支持为行业发展保驾护航
我国高性能碳纤维持续突破。除了大丝束方向的发展,我国碳纤维在力学 性能方面也在进步,国内涌现出如中复神鹰、光威复材、中简科技等在小 丝束领域有技术积累的企业。例如中复神鹰在国内率先建成干喷湿纺 T700 级、T800 级碳纤维千吨级生产线,相继开发出 T700、T800、T1000、 M30、M35、M40 等级别的碳纤维,并规划了下一代 T1100 级碳纤维的研 发;光威复材已开发出 T300、T700、T800、M40J、M50J 等型号的产品, 其中去年投产的 M40J、M55J 产品实现了国产高强高模碳纤维的突破;中 简科技于 2020 年投产的 T700 级碳纤维千吨线可批量稳定生产 ZT7 系列、ZT8 系列、ZT9 系列高性能碳纤维,募投的 1500 吨 12K 产线还将探索、 M40J、M40X 和 M55J 等新的型号。
我国加大对碳纤维产业的扶持力度。随着我国产业结构升级,政府加大对 新兴产业等尖端技术密集产业的扶持力度,碳纤维作为用途广泛的新材料, 得到了众多政策支持,国内企业迎来机遇。
四、碳纤维的制备工艺:原丝和碳化
碳纤维的工艺路线主要分位上、中、下游三个阶段。上游为原丝的制备: 通过对丙烯腈聚合,后经纺丝形成碳纤维原丝;中游为碳纤维的生产:对 原丝进行预氧化、碳化、表面处理等制备碳纤维;下游为复合材料及制品 的加工:一种是绕卷形成碳纤维丝束直接使用,另一种是上浆、编制后与 基体材料复合成型,得到碳纤维复合材料。
碳纤维生产技术上存在配方壁垒、工艺壁垒及工程壁垒,难度依次增加。 根据光威复材的公告,配方只要通过购买配方或者挖角技术人员等方式即 可获取,获取后可迅速消化吸收,壁垒突破时间为 1-2 年;工艺需要在拥 有配方的基础上,配合生产装备、技术人员进行不断的工艺调整和磨合, 最后才能工业化生产出合格的产品,例如原丝生产过程中的蒸汽牵伸工艺, 工艺壁垒突破时间为 3-5 年;多道生产工艺组成了全套工程体系,工程体 系需要每个生产工艺之间的协调配合,并需要企业的装备设计、改造和调 整能力,对技术人员要求更高,需要企业大量的资本投入。工程壁垒突破 时间 5 年以上。
4.1 碳纤维原丝环节:聚合-纺丝
原丝制备是碳纤维制备中技术壁垒最高的环节,直接决定碳纤维产品的质 量和成本。原丝制备包括聚合和纺丝两个环节,聚合是将丙烯腈单体聚合 成纺丝液,纺丝是将纺丝液经过喷丝、凝固、成型等工艺制成原丝,纺丝 决定了原丝的性能。
丙烯腈聚合:按聚合工艺不同可分为一步法和二步法。聚丙烯腈(PAN) 是由单体聚丙烯(AN)经过自由基聚合反应得到的高分子材料,按照聚合 方法不同可分为均相溶液聚合和水相沉淀聚合。均相溶液聚合的单体、引 发剂以及聚合产物均溶于溶剂,所获得的 PAN 纺丝原液经过脱单脱泡后, 可直接应用于纺丝,故又称为“一步法”;水相沉淀聚合属于非均相聚合工 艺,以水为反应介质,反应单体可溶于水,而反应所得的聚合物不溶于水, 沉淀后得到的 PAN 粉末在纺丝前需经溶剂再次溶解成纺丝原液,故而称为 “二步法”。一步法的聚合转化率高,工艺流程短,有利于提高原丝产品质 量,是小丝束主要采用的工艺,二步法中聚合釜的生产能力较大,且聚合 热的移除效率也较高,适合生产大丝束。
纺丝:目前主流的纺丝方法有湿法纺丝和干喷湿纺。通过聚合工艺得到纺 丝原液后,纺丝原液进入纺丝工段,包括纺丝(纺丝原液通过喷丝帽进入 凝固浴)、水洗与整理(热水牵伸、上油、蒸汽牵伸)和组件喷丝板准备 (清洗)等过程形成 PAN 原丝。根据纺丝过程中喷丝帽与凝固浴液面之间 是否存在空气层介质,可将纺丝工艺分为湿法纺丝和干喷湿纺。湿法纺丝 是原丝液从喷丝头喷出直接进入凝固浴,干喷湿纺是原丝液从喷丝孔出来 不直接进入凝固液,而是先经过一段空气段。干喷湿纺的优点在于其喷丝 时表层没有接触到水,因此表层和芯部的收缩率一样,产生的缺陷较少, 进而导致最终碳纤维强度更高,此外,干喷湿纺可以进行高倍速喷丝头拉 伸,纺丝速度是湿纺的 3-4 倍,但是干喷湿纺的单锭线密度较低,不能实 现大产能,同时也不适用于大丝束碳纤维原丝制备,因此干喷湿纺主要适 用于小丝束生产,湿法纺丝则适用于大丝束生产。
油剂:碳纤维原丝纺丝及后加工处理的重要助剂。原丝在纺丝阶段需 要上油,主要作用是保护纤维表面不产生热粘连或热融并现象,使原 丝能顺利通过预氧化与低温碳化等过程。油剂是国产碳纤维向更高强 及高模方向发展时必须解决的一项核心技术,油剂质量不过关就在生 产中造成原丝劈丝、粘连及表面损伤。高性能碳纤维油剂多为硅系油 剂,目前我国与海外差距较大,且成本很高,根据赛奥碳纤维的数据, 油剂的降本可以将原丝单吨成本从数千元降低到数百元。
4.2 碳纤维碳化环节:预氧化-碳化-表面处理-上浆
得到原丝后,需要对原丝进行碳化处理以去除材料中的非碳元素,使其含 碳量超过 90%。主要流程包括将卷绕好的聚丙烯腈原丝进行退丝,以提高 丝线的强力和耐磨性,然后通入氧气进行预氧化,原丝经预氧化处理后转 化为耐热梯形结构的预氧丝(PANOF),再经低温碳化和高温碳化转化为 具有乱层石墨结构的碳纤维(CF),随后经表面处理后进行上浆,最后经 烘干得到碳纤维产品。
预氧化:预氧化是制备碳纤维非常重要的一个环节,是承接原丝与碳纤维 之间的桥梁。原丝在大约 200-280℃范围内,经脱氢、环化等过程,使线 型分子链转化为耐热的梯形结构,使其在碳化的高温下不熔不燃,能够保 持纤维结构。
碳化:碳化是乱层石墨结构形成、长大和有序化阶段,是碳纤维拉伸强度 大幅提高的阶段。碳化过程分为低温碳化和高温碳化两个阶段,低温碳化 的温度控制在 300-1000℃,预氧丝在热解作用下将 CO2、H2O、CO、 HCN、NH3 等裂解出去,随后丝束进入高温碳化炉中,在 1000-1700℃的 高温下,大分子进一步交联,使原来梯形分子结构转变为乱层石墨结构, 非碳原子逐步排出,最后形成含碳量 90%以上的碳纤维。
表面处理:显著改善纤维和基体树脂之间的界面结合力,使负荷剪切强度 ILSS 提升到 90MPa 以上。碳纤维增强树脂(CFRP)作为工程结构材料 使用时,要求曾间剪切强度(ILSS)在 80MPa 以上,最好在 90MPa 以上, 经过表面处理的碳纤维 ILSS 可提高到 80-120MPa,可满足使用要求。工 业上常用的表面处理方法主要有阳极电解氧化法和气相氧化法等。
上浆:经过上浆处理的碳纤维,其表面空隙减少,纹理沟槽变浅,可以减 少碳纤维的损伤,力学性能有一定程度提高。在碳纤维表面直接涂覆一层 高分子材料以改善碳纤维表面性质的工艺被称为上浆,对应的高分子材料 被称为上浆剂。商业上常用的上浆剂为尼龙与环氧树脂等原料以一定比例 配比而成。根据《大丝束碳纤维发展现状及我国技术瓶颈和发展建议》一 文的介绍,上浆剂是我国碳纤维生产商的重要技术短板,各家的上浆剂配 方实行严格保密和技术封锁。
五、投资分析
5.1 吉林化纤 :供应链配套完善,大丝束产能快速扩张
碳纤维产业链配套完善,布局小丝束与复合材料业务。公司是吉林化纤集 团旗下的上市公司,传统主业为粘胶长丝和粘胶短纤。2021 年 2 月公司的 子公司吉林凯美克宣布将引进设备生产 600 吨 1K、3K 小丝束碳纤维产品, 公司正式进军碳纤维领域,2022 年 6 月该项目已全部建成达产。2021 年 9 月,公司启动 1.2 万吨碳纤维复材项目,生产风电叶片拉挤板等材料,项 目预计年内投产。由于吉林化工集团旗下的吉林碳谷是国内重要的原丝供 应商,故而公司碳纤维产业链下游所需原材料均可通过吉林碳谷供应,产 业链配套十分完善。
吉林国兴三年内有望装入上市公司,大丝束碳纤维产能快速扩张。吉林国 兴碳纤维成立于 2008 年,2020 年 5 月正式划归吉林化纤集团旗下,并成 为集团实施大丝束碳纤维项目的主体。2020 年 8 月国兴碳纤维开始实施 1.5 万吨大丝束碳纤维项目,自 2021 年 7 月第一条大丝束产线投产以来, 公司累计投产近 10 条大丝束产线,并于今年 7 月开启 6 万吨 35K 以上大 丝束碳纤维项目,未来大丝束的名义产能有望达到 7.5 万吨。2022 年 3 月, 集团承诺 3 年内将采取包括将国兴碳纤维股权注入上市公司在内的符合国 有资产监管、证券监管的相关举措,未来优质资产有望注入。
5.2 中复神鹰:高性能碳纤维龙头企业,布局航空航天与新能源领域
技术实力突出,产品偏高端化。公司是国内第一家突破干喷湿纺技术的企 业,产品应用于航空航天、风电叶片、压力容器、碳碳复材等领域,2021 年上半年公司在上述领域的收入占比分别为 14%、15%、11%、22%。公 司目前具有一定规模的 T300、T700、T800 和 M30 的碳纤维生产和销售 能力,具备了在航空航天及重点工业领域推广应用的条件,其中 T700 级 和 T800 级高性能碳纤维产业化的千吨级碳纤维生产线已经投产,后续公 司计划建设航空航天高性能碳纤维及原丝试验线项目,用于下一代 T1100 级碳纤维研发,进行航空航天用高性能碳纤维的应用技术开发、产品应用 认证和生产。
西宁项目有序投产,产能逐步释放。公司在西宁基地建设的一期万吨级碳 纤维项目已于去年 9 月份投产,二期 1.4 万吨碳纤维项目预计将于 2023 年 陆续投产,届时结合公司在连云港基地 3500 吨的原有产能,将有效满足 航空航天、新能源、交通建设等下游应用领域对高性能碳纤维的需求。
5.3 光威复材:全产业链布局,军品民品双轮驱动
公司布局全产业链,产品种类丰富。公司业务涵盖碳纤维、经编织物和机 织物、系列化的树脂体系、各种预浸料、复合材料构制件和产品的设计开 发、装备设计制造等上下游,依托在碳纤维领域的全产业链布局,成为复 合材料业务的系统方案提供商。公司目前已形成高强、高强中模、高强高 模系列化碳纤维产品体系,并建设了先进碳纤维复合材料研发中心碳纤维 牌号涵盖 T300、T700、T800、M40J、M55J 等型号,并拥有自己的原丝 产能。
航空航天领域持续突破,包头项目预计今年投产。2021 年公司 IPO 募投 的高强高模型碳纤维产业化项目正式批产,M40J、M55J 产品实现了国产 高强高模碳纤维的突破;军民融合高强度碳纤维高效制备技术产业化项目 年产 2000 吨 T700S/800S 级碳纤维也于去年二季度投产;T800H 级航空 应用项目验证工作碳纤维研制环节的任务在去年基本完成,现有 105 吨产 能的产线能够满足验证及小批量交付需求,同时开展产业化生产线等同性 验证工作。为满足供应 Vestas 的碳梁的原材料自给,并在新能源等民品领 域加大布局,公司在包头建设的万吨级大丝束产业化项目一期 4000 吨预 计将于今年内投产。
后疫情时代业绩有望加速向上,股权激励显示长期成长信心。根据公司发 布的业绩预告,2022 年上半年公司实现归母净利润 5.06 亿元,同比增长 16%,二季度克服疫情影响,归母净利润环比增长 43%,随着国内疫情的 逐步消退,公司中长期业绩有望加速向上。今年上半年公司实行新一轮股 权激励计划,以 2021 年为基数,2022-2025 年的目标净利润同比增速分 别为 15%、22%、21%、17%。
5.4 中简科技:聚焦小丝束高端产品,供应航天军工
公司为国内高端碳纤维厂商,主要供应航空航天军工。公司主要从事高性 能碳纤维的研发和生产,产品主要供应于航空航天领域,其 ZT7 系列高性 能碳纤维产品在国家航空航天关键装备的稳定批量应用。公司还拥有 ZT8 系列(T800 级)、ZT9 系列(T1000/T1100 级)和高模型 ZM40J(M40J 级)等产品。公司产品主要军用,用于高附加值的航空航天领域,所以毛 利较高。
千吨线通过等同性验证评审,三期项目预计 2024 年投产。公司 IPO 募投 的 1000 吨/年国产 T700 级碳纤维扩建项目(简称“千吨线”)于 2021 年 9 月通过了客户及相关部门产品等同性验证程序,进一步提升了航空航天 高性能碳纤维供给能力,另一方面,公司新增了碳纤维织物设备,2021 年 碳纤维织物产能较 2020 年相比提升了 2 倍。今年 1 月,公司拟募集资金 建设三期项目,建成后具有年产 1500 吨(12K)高性能碳纤维及织物产品 的生产能力,项目包含 2 条碳化线,其中一条主要用于生产 ZT7 级碳纤维, 另外一条生产线主要生产包括 ZT8、ZT9、M40J、M40X 和 M55J 等型号 在内的新一代国产高性能碳纤维,项目建设期 4 年,预计于 2024 年投产。
(本文仅供参考,不代表我们的任何投资建议。如需使用相关信息,请参阅报告原文。)
精选报告来源:【未来智库】。